在德州工厂“开业Party”的时候,Elon Musk提到了一个很重要的地方,就是关于生产基地的问题。
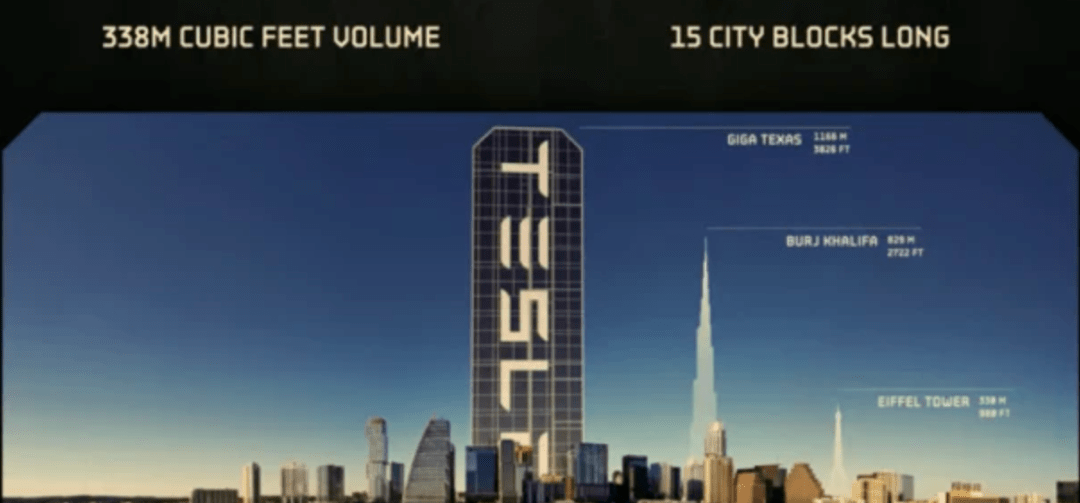
图1 特斯拉的工厂
从整个特斯拉的发展路径来看,核心是“更容易和更快速的去制造一台车”。不管是一体化制造、线缆变短,本质其实还是在设计之初就要考虑在工艺上进行系统性改革。能够在整个制造效率上,让整车供应链变短,整车的制造用时和运输用时变少,用的人工变少,然后让几个制造基地快速撑起巨量的制造规模。
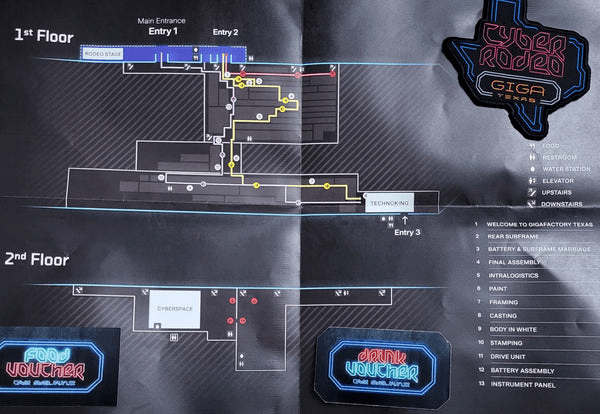
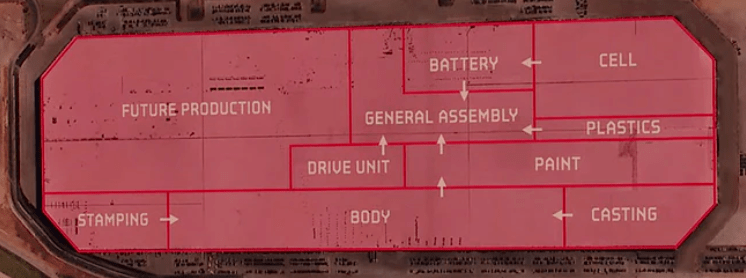
图2 德州工厂开业当天的参观路线和开放的区域
根据前几天微博上传出的“特斯拉的Roadmap”来看,特斯拉产品量的核心还是这么几台车,最多从皮卡扩展到Van,目前更多的还是集中在“S、X、3、Y”,另外就是车型平台会有Model E这种新版本的扩展。
备注:特斯拉对产品线的扩展到底会有多快?总体来看,很克制。
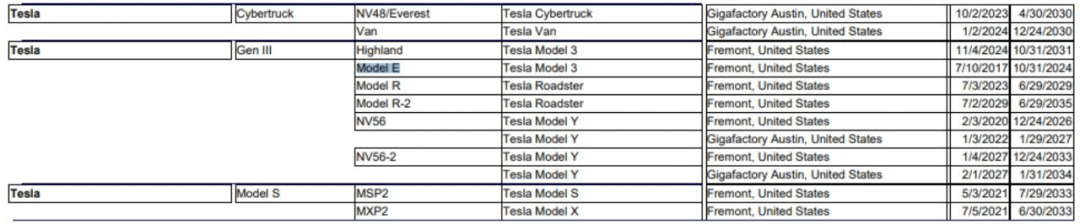
图3 AFS 预测的特斯拉产品规划和美国制造基地分布
Part 1:一体化铸造
2021年3月推出的一体压铸后底板,把70多个零部件减到最少,这是对传统冲压焊接工艺进行重构。也就是说,在成功推出之后,汽车行业都认识到这种投入巨大的设计,在成本经济性、工艺流程和生产节拍、材料利用率等方面具备较强优势。国内新势力企业,包括蔚来、小鹏、理想都在研究,而沃尔沃、奔驰等相关全球性企业,也在思考之前的工厂是否能符合下一代电动汽车制造效率的节奏。
(备注:沃尔沃作为传统车企的代表,第一个推进一体压铸厂房改造和底盘一体化结构件。)
主要的优点包括——
1)成本经济性提升:钢制白车身的质量在300-400kg左右,铝材料代替钢材料可以减轻重量30-40%,从材料价格和循环使用的角度,铝压铸车身可以在长周期维度做到与钢制车身平价的水平,兼顾轻量化和成本因素。更重要的是,零件的制造费用也将得到改善。
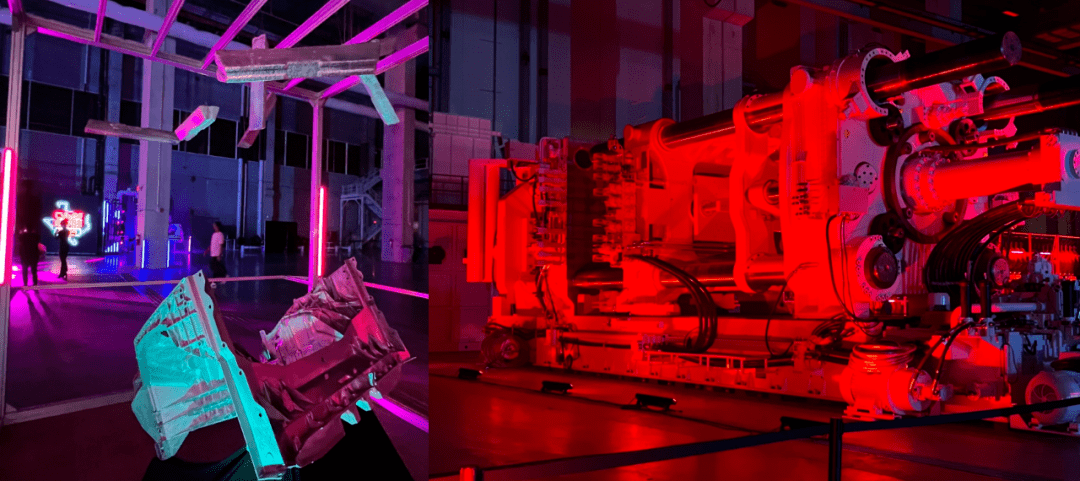
图4 制造的成本和节奏
2)整车生产节拍优化和工艺流程简化:整车制造流程和工时将通过一体成型得到明显的优化,以特斯拉的
Model Y(参数|图片)为例,后底板工艺的切换从1-2小时的工时减少到3-5分钟,随着扩展到前部和电池托盘,整个整车制造压铸机设置单独工位,只需要中转仓库就可以满足单台设备全天24h无休,也支持德州工厂单线50万台年产能。
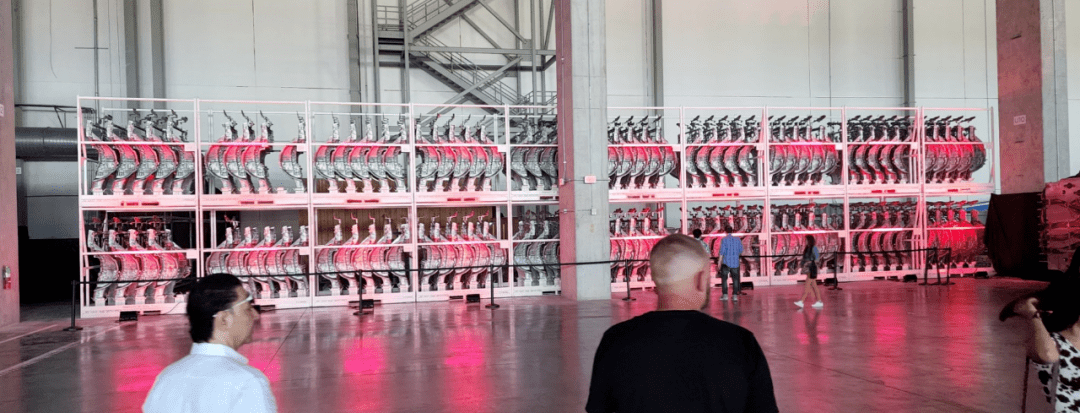
图5 中间结构总成的中转也简单了
3)产品复杂性:这方面特斯拉在之前有过展示,Model Y的设计和制造,有希望在设计和制造上实现一体化,不光是把焊点减少,整个产品总成的复杂度得到简化,把供应链环节直接缩短了。
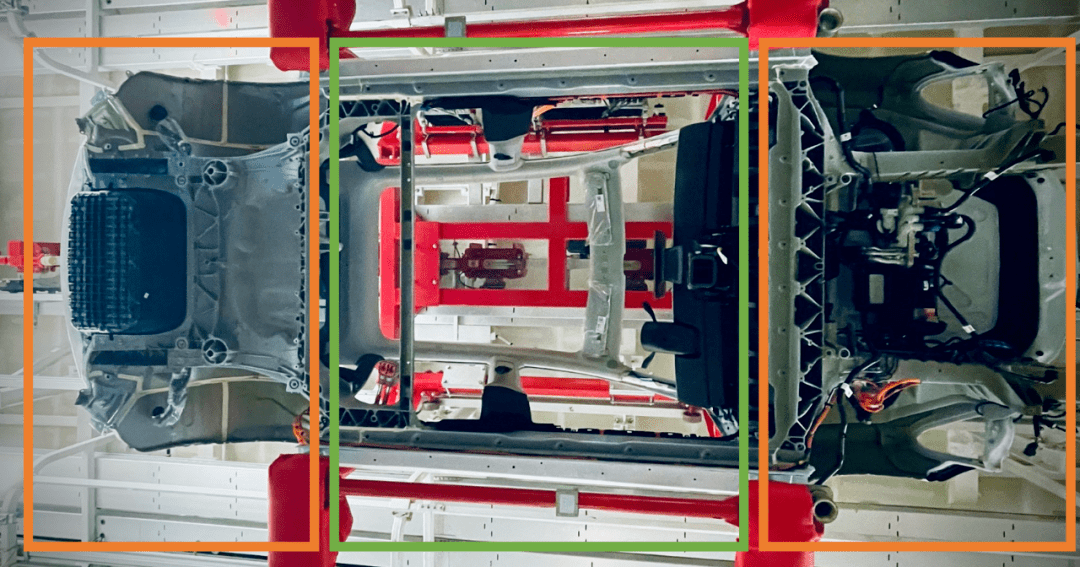
图6 复杂度在持续降低,结构上越来越简化
4)可持续发展,材料利用率提高:关于压铸熔炼材料和回收铝,我的理解是,特斯拉的“生意模式”变成可回收的——整车“退役”了,把车交给它、电池交给它,通过处理给你再做一台出来,这种思考方式为汽车行业打开了一条新思路。
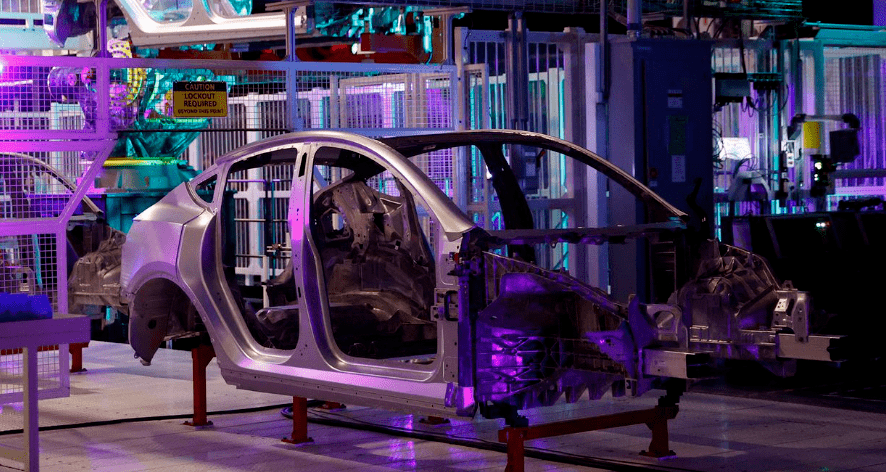
图7 车辆本体和电池材料将来都能回收,整个生命周期都是永续的
在电动皮卡上采用锁模力达到8000T的Giga Press压铸设备,这个新兴车辆的黑科技比较多,也需要加速生产节拍和简化生产复杂度,将整个下车体总成进行一体压铸,包括后底板总成、前舱总成等都进行工艺替换,大幅度提升生产制造效率。这对于电动汽车的发展,是物理骨骼上的变化,我觉得很有意思。
Part 2:高低压线束
如下面图9这个吊起来的线缆,尽管Model Y的100米更像是一个梗,但是从整体的设计来看,目前高低压线束都在简化。随着高压系统集成化(PTC逐渐被边缘化),DCDC和OBC集成化。整个高压系统,必要的连接是——
1.直流充电输入接口(1对),外部是充电枪;
2.电池包快充接口(1对),充电用;
3.电池包放电接口(1对),后驱动用;
4.电动压缩机输入接口,这个存疑,可能将来(3-5年)和驱动系统集成在一起;
5.DCDC,输入接口存疑,现在已经部分没有了;
6.OBC,在ET7上已经被拿走了;
7.驱动系统:输入一对,如果是四驱系统拉的线会长一些,在
Model S(参数|图片) Plaid里面走铜排设计的方式。
所以可以算算,以后高压后驱系统的话,整个高压连接主要是围绕电池包的2对必不可少,其他都在集成化中被简化了。
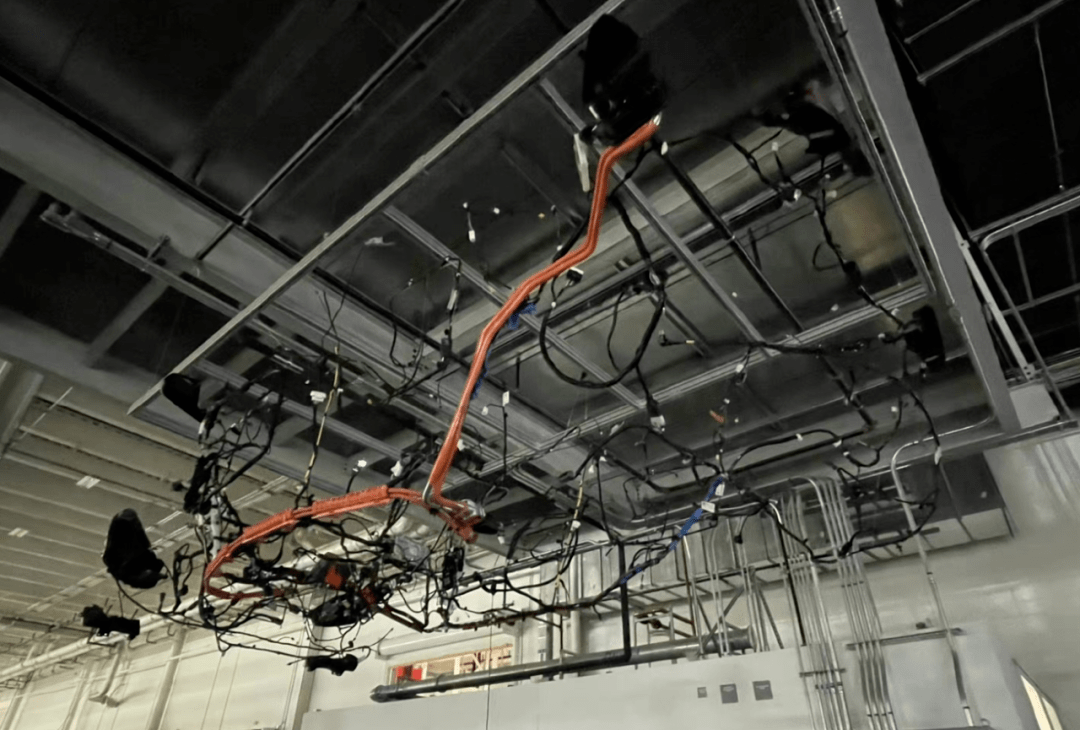
图8 特斯拉的高压线束
特斯拉的低压控制器和整体的负载也在不断的简化中,目前来看各种灯、电机因复杂很难被优化,集成化的控制线路更可能把功能合并,我觉得终极就是电源供给和信号控制优化,部分无线化。总之在智能化的道路上其实多种路径都在发展。
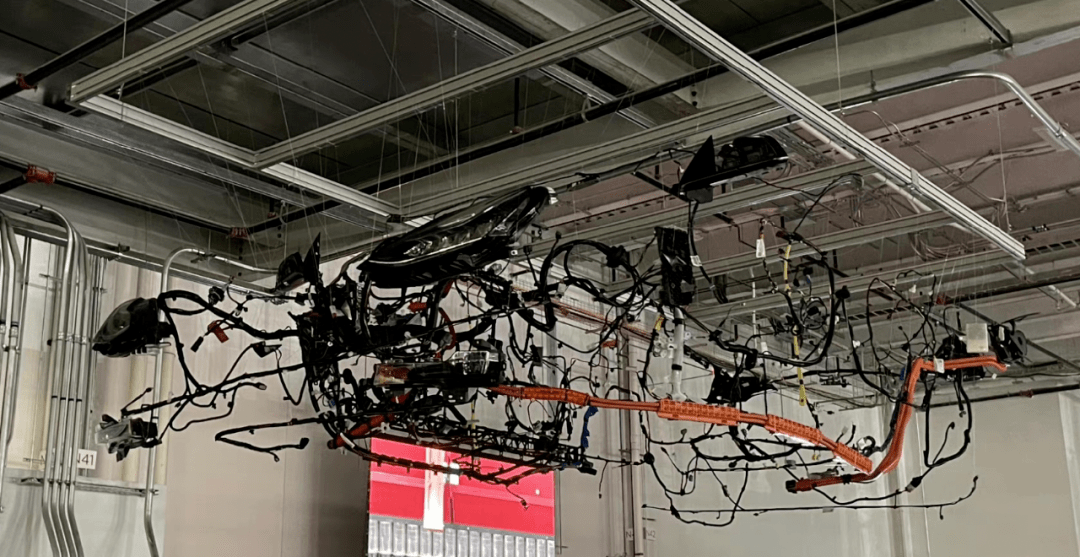
图9 特斯拉的线束设计
小结:
我觉得新势力的产能门槛是50万台,就像电池企业要爬到20GWh、50GWh这样的门槛点,汽车制造和电芯制造都在努力做简化,回归合理性。除开软件,汽车制造里面的重构怎么去找合适的爆点,也是需要去持续思考的。