汽车线束疲劳断裂分析及应对方案设计
发布时间:01/25 —— 2022
3490
线束的金属导体(铜丝)在交变应力作用下(振动或者运动件产生),应力值虽然始终没有超过材料强度极限,经过长时间的应力反复循环作用以后,导体发生突然脆性断裂。如图,手机充电线束尾部在长期使用,由于插拔时接口尾部线束受到扭曲弯转的应力,外护套首先开裂(外护套材质多为TPE),然后继续使用就会出现导体铜丝疲劳断裂。那么研究充电线的耐折弯性能对改善充电线束的使用寿命变得尤为重要。下方图片是疲劳断裂的导体断口位置的微观形貌,疲劳端口多发生在硬度差异的结合处,如上图充电线的圆圈位置,汽车线束线束固定卡扣的固定位置,导体会在长期挤压的位置形成凹痕,导体单丝之间会有相互运动产生的摩擦痕迹,一般导体断口位置会有一定的氧化。手机充电线束的断裂只是影响我们手机充电,再借条充电线不影响我们看公众号、刷抖音,但作为汽车线束就大不相同,汽车线束作为高、低压电气/器部件的连接载体,承载整车的动力、信号传输,主导着整个汽车的安全与性能,汽车的载体是人,安全和客户感受尤为重要,。线束疲劳断裂是线束的主要失效模式之一,汽车的车门线束、后背箱线束、发动机线束、车速传感器线束、新能源汽车的驱动电机线束(特别是轮边电机)、打气泵线束、空调压缩机线束等,在使用过程中承受弯曲载荷和振动载荷,恶劣环境下还要承受热载荷。当这些汽车线束被运动或振动部件做周期性运动时,如果设计不合理,电缆耐弯曲性能不足,导体铜丝部分或全部会出现断裂、断股问题,就会影响车辆的正常功能及安全,目前整车对于导体断裂没有较好的检测手段,只有在线束导体完全短路、断路故障才能检测。如果是新能源汽车高压线束突然发生短路,可能出线拉弧,对线束及电气部件甚至是整车造成不同程度的危害。导体材料(铜 )加工工艺控制不合理 ,拉丝或退火过程中导致铜过度氧化而发脆 ,或者是挤绝缘后的硫化过程中由进水或与高温分解出来的酸性物质反应使导体铜丝表面发黑 ,从而降低铜丝的韧性,一般汽车电缆导体使用含铜量99.99%的无氧铜。绝缘或护套材质问题,机械物理性能差,耐老化性能差,没有足够的伸长率、抗张强度、拉伸回缩率,绝缘和护套对线芯和导体支撑不足。如撞击、机械冲击,线束短承受拉力,以下刹车报警线束过短,打方向会把这根线崩的特别直,时间长了线束从里面断了,外表看不出来任何问题。4.电缆耐弯曲性能、线束的布置结构不能满足实际工况的需求电缆的耐弯曲性能和导体的单丝直径、导体的绞合结构、电缆结构有关系。
目前我们在用的新能源汽车高压线束导体单丝直径按照QC/T 1037选取,一般单丝直径为0.21mm,如果想改变现有导体的弯曲性能可以选取更小的单丝直径,如0.15mm;
一般情况下,一次束绞导的节径比不得超过 25,如是复绞线 ,则股线绞合节径 比应不大于30,而内层和外层绞合节径比分别应不超过 2O和 14。大节距的铜线远比小节距的铜线要硬 ,其允许的最小弯曲半径会增大;为了延长振动或运动部件电缆的使用寿命,必须尽可能地提高导体的柔软性,而组成导体的单线越细,导体的柔软性则越高;然而单线的粗细与其机械强度及承荷能力有直接关系,单线越细其承荷能力越差, 为了解决这一矛盾,可以先将多根单线束绞成股线,所有股线绞合方向相同,再将多股股线复绞成导体,复绞时相邻层股线复绞方向相反,确保绞合导体的柔性,及机械强度。避免铜丝氧化 首先应选择合理的加工工艺 .铜丝可采用连续退火的方法 ,若非要二 次退火 ,则退火炉的无氧纯度要控制 。其次是应降低硫化过程中的水汽和硫化反应 产生的副作用正常情况下 (除个别本身挤橡工艺缺陷外 ), 水汽的副作用不是太明显 ;而由于配方物质高温分解出酸性物质所致的梳化反应可通过提高橡胶配方的热稳定性加以解决 ,同时 ,避免硫化温度过高是其较为有效的方法 .当然这并不意味着要求将温度降低硫化点以下 控制绞合节径比在束 、绞线芯时 ,理论节径比要适当小些 ,一般可比标准值下调 1O%~ 15% ,这样才能使实际节径比最终与 标准规定的上限值接近同理 ,对于成缆绞合节径 比的控制也如此 。控制绝缘和护套胶料的含量绝含胶量应控制在 35%以上 ,而护套胶的含胶量应 不低 于 42%,这是基本要求 。当然影响材料的抗张强度 、 长率和拉伸回缩率的还跟配方组成和炼胶工艺及硫化工 艺有关 ,良好的护套胶 ,其抗张强度应在15N/ mm以 上 (标 准值 为 11N/ mm:).其伸长率也达 500%以 上。柔性耐弯曲电缆在弯曲时(缆芯会承受相应的 拉伸力和压缩力,缆芯中处于弯曲顶部的绝缘线芯承受拉伸力,绝缘线芯位置外移(处于弯曲底部的绝 缘线芯承受压缩力,绝缘线芯位置内移(越靠近弯曲的边缘(受力越大,绝缘线芯间的相对移动越大- 当电缆弯曲消失归复原位时(缆芯承受的拉伸力’压缩 力消失(绝缘线芯位置也应复原- 电缆频繁弯曲时绝缘线芯也高速重复滑移(达到复原补偿效果- 如 果电缆内部缆芯的结构不够稳定(缆芯不够圆整,就会导致绝缘线芯间滑移补偿性差甚至绝缘线芯间 出现内嵌卡死现象进一步恶化的结果就是绝缘线芯断芯- 另外(缆芯承受的拉伸力越大(缆芯结构 越不稳定,出现缆芯变形的几率也越大缆芯弯曲应力示意图 为了提高电缆内部缆芯的结构稳定性,摒弃了以往使用的 PP填充绳、麻绳、棉绳填充条等填充材料,改用绝缘材料挤制填充条,并且在填充条的中心放置芳纶线替代柔性碳素钢丝绳,放置在缆芯 的中心位置的芳纶线填充条,既提高了填充条的载荷能力,降低绝缘线芯受到的拉伸力,又增强了缆芯的整体柔软性’结构稳定性圆整性,从而使缆芯具有更佳的耐弯曲性能和耐扭转性能。柔性耐弯曲电缆缆芯外一般不绕包包带,绝缘线芯与护套紧密接触-,为防止护套与绝缘粘连,不利于电缆的剥离,一般在缆芯外涂覆滑石粉,但滑石粉易吸潮结团,容易出现线芯表面涂覆不均匀,在线 芯间隙中积累过多,线芯表面少容易在模芯内洒落 累积,被缆芯带出致使电缆起包,干燥的滑石粉容易 扬尘,不利于卫生清洁,并且对人体有害,用滑石粉进行绝缘与护套隔离的柔性耐弯曲电缆,由于滑石粉涂覆不均匀,在弯曲过程中,绝缘线 芯间的滑移补偿也不均衡(影响电缆的使用寿命(因 此在绝缘线芯挤制时在线芯绝缘表面涂覆液体隔离剂-绝缘线芯浸没在隔离剂中使其表面均 匀涂覆,利于绝缘线芯间的相对滑移确保线芯在弯 曲过程中滑移补偿均衡,以进一步提高缆芯的耐弯 曲性能。绝缘挤包使用挤压式模具,使绝缘层紧密包覆在导体外面,增强绝缘层与导体间的附着力- 挤包 过程中,绝缘层若出现划伤’: 形弯’火花击穿等不良现象,不允许对绝缘线芯进行修复处理,尽可能消 除绝缘线芯的质量隐患,外护套改进外护套在柔性耐弯曲电缆中具有非常重要的作 用它不仅起到保护绝缘线芯的作用,还会承受极大的载荷弯曲应力因此柔性耐弯曲电缆的外护套一般极高抗拉强度’抗撕裂强度优异的耐磨性能耐老化的材料,如TPU。 我在前边有一一篇介绍ModelY实车高压线束视频解析,ModelY实车高压线束视频解析,里边讲了对其热泵线束疲劳断裂的担心“一个是从视频中我们看到热泵是有胶垫减震的,晃动量挺大,需要选用耐振等级更高的插件,由于有注塑支架固定线束随热泵一块振动,此处担心还不是很大,担心较大的就是不知道特斯拉设计时有没有考虑到此电缆在绿色框处可能存在疲劳断裂风险,对电缆进行了针对性的设计,从视频中看热泵振动较大,此处余量也不是很多,导体可能存在疲劳断裂的风险。”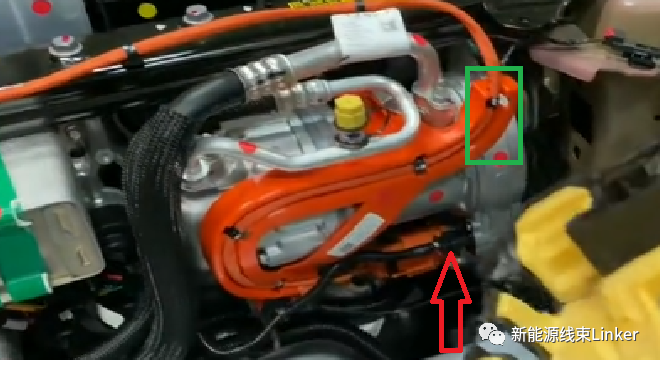
轮边、轮毂电机高压线束,由于电机线束一侧在轮子上,另外一端在车架上固定,且乘用车空间有限,车轮反复跳动,如果电机线束设计不合理,电机线导体存在断裂风险。
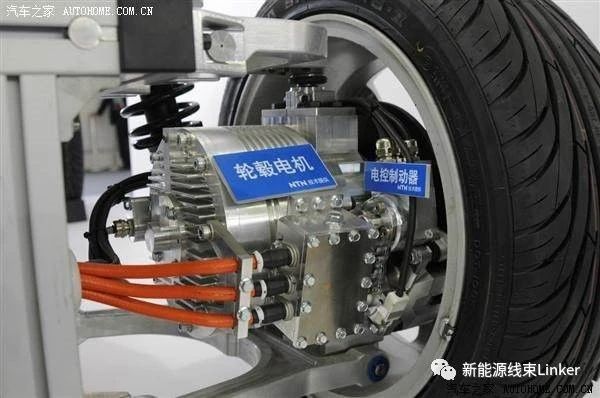